Over the weekend, Rachel harvested 3.5 pounds of Concord grapes and made jelly! I’m having some on biscuits now. So cool!
Easily my favorite, most used flea market tool is a Klein folding rule. Sturdy, compact, and better than a tape measure in several ways. And the solid feel when each section snaps into place is satisfying. 😄
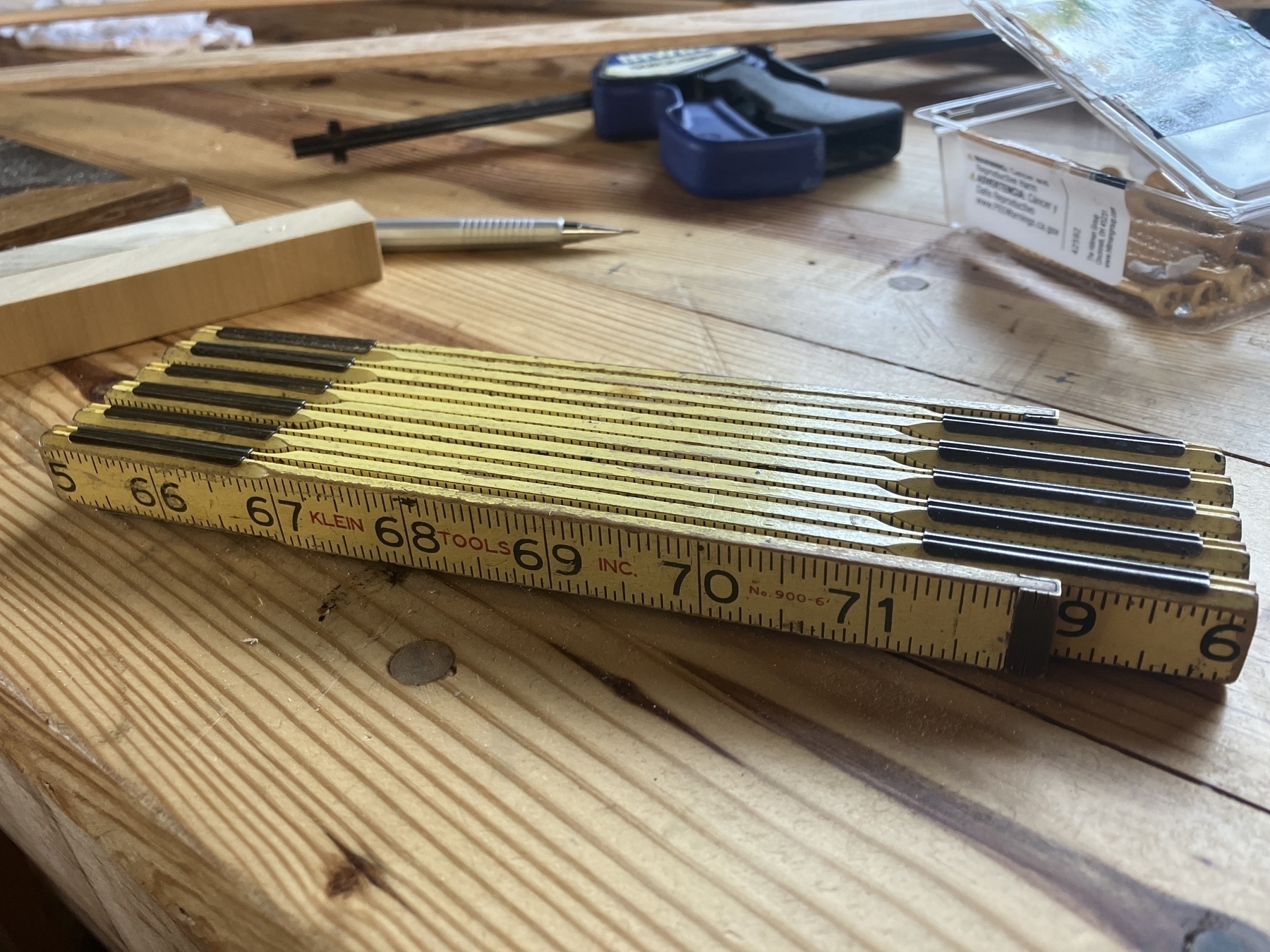
Two unlikely dreams re: the Bedford pie safe:
- Acquire one of the 16-20 known to exist and preserve it. Something this unique shouldn’t be allowed to vanish.
- Build a reproduction. I will never have the skill of an actual 19th century professional cabinetmaker but it would be a heck of a project.
Pickled some banana peppers tonight. Should be about a week until they’re ready to eat.
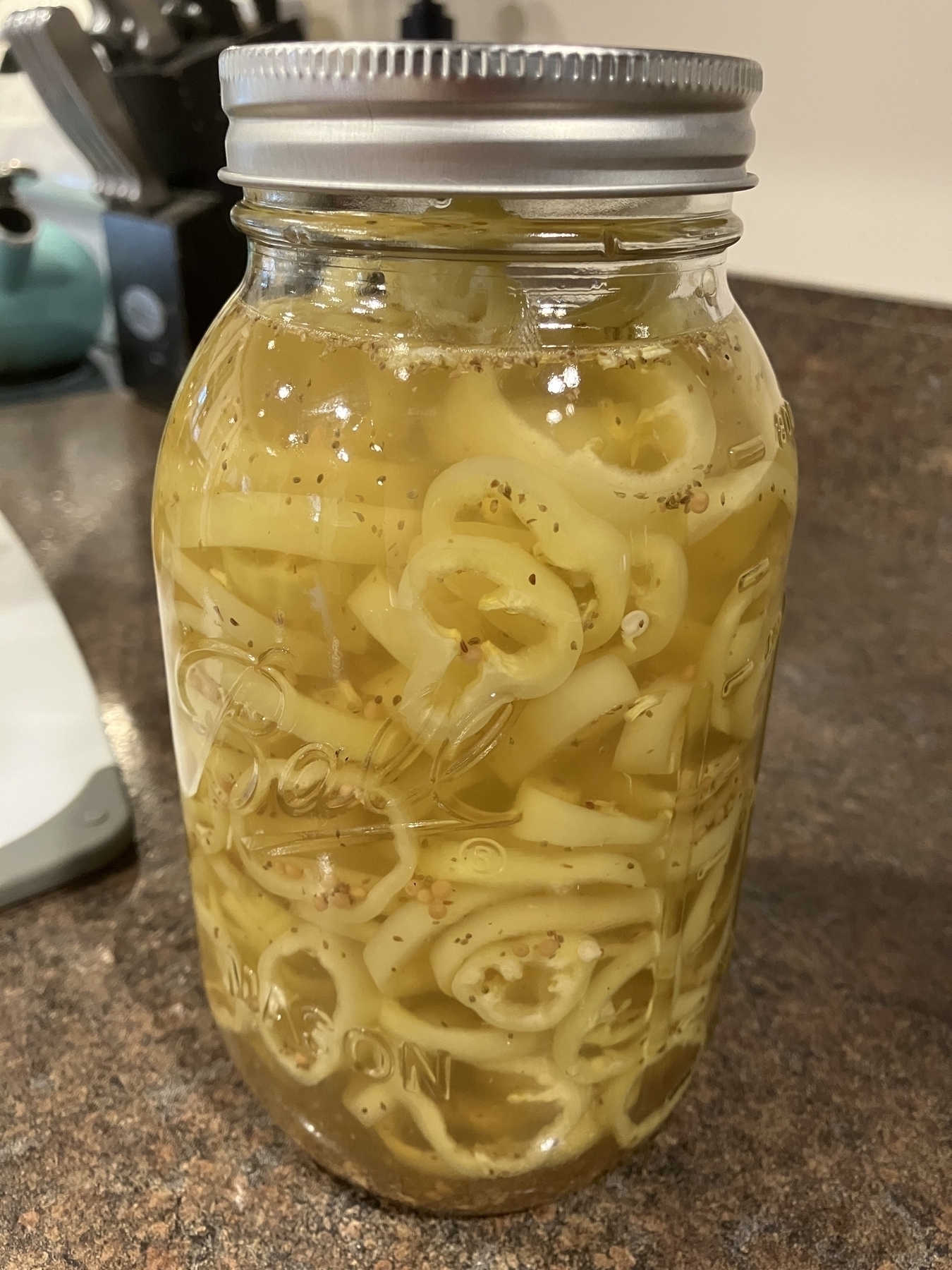
Work has begun on my next project: building a cabinet for a friend. It’s in trade for some of his grandpa’s tools. He already had the countertop so I’m building the carcass and attaching it.
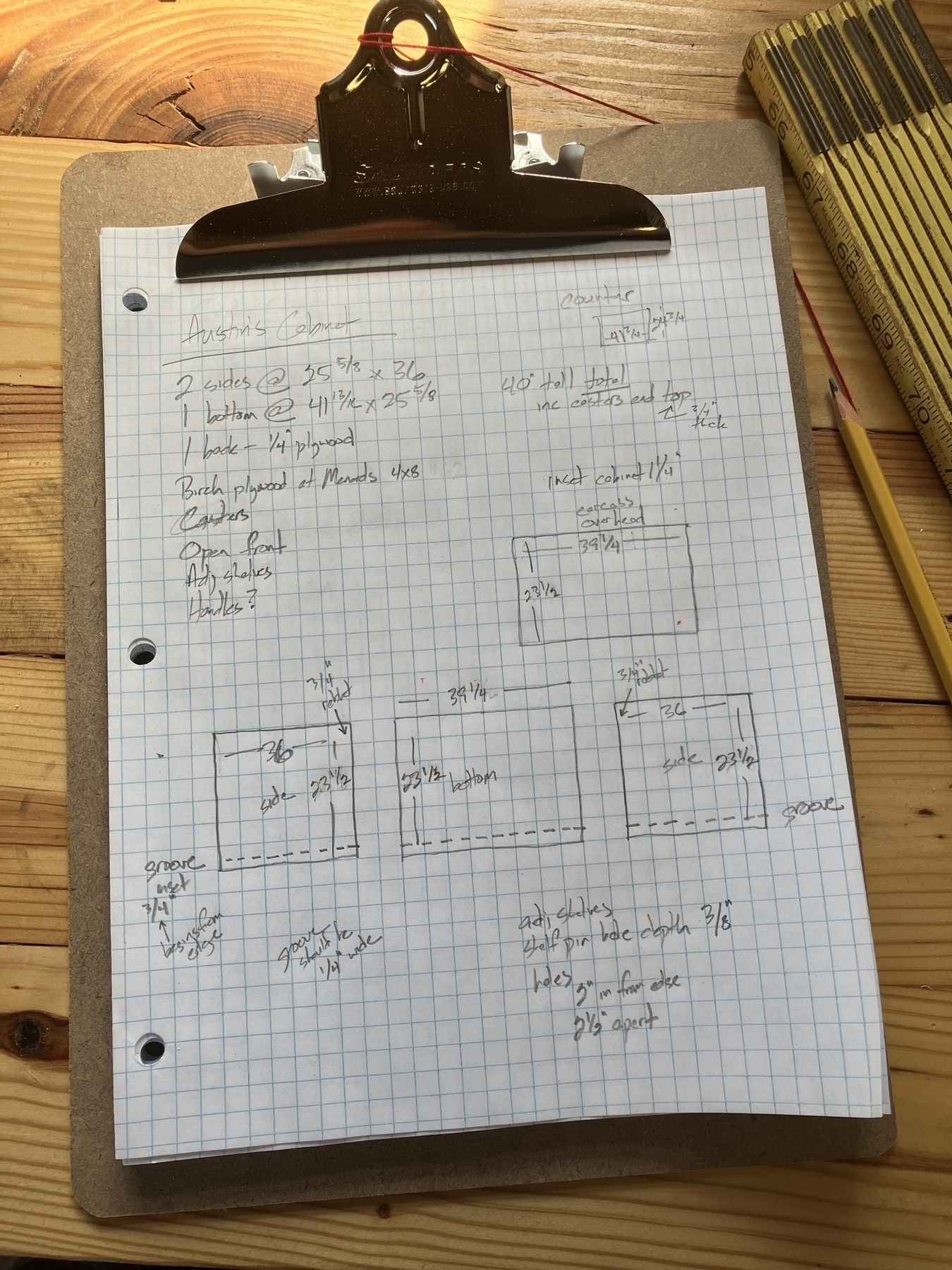
Before and after on the table and chairs refinishing project for my in-laws. I have one chair (not shown) I’m going to start over. Apart from that, I think I’m done.
Before:
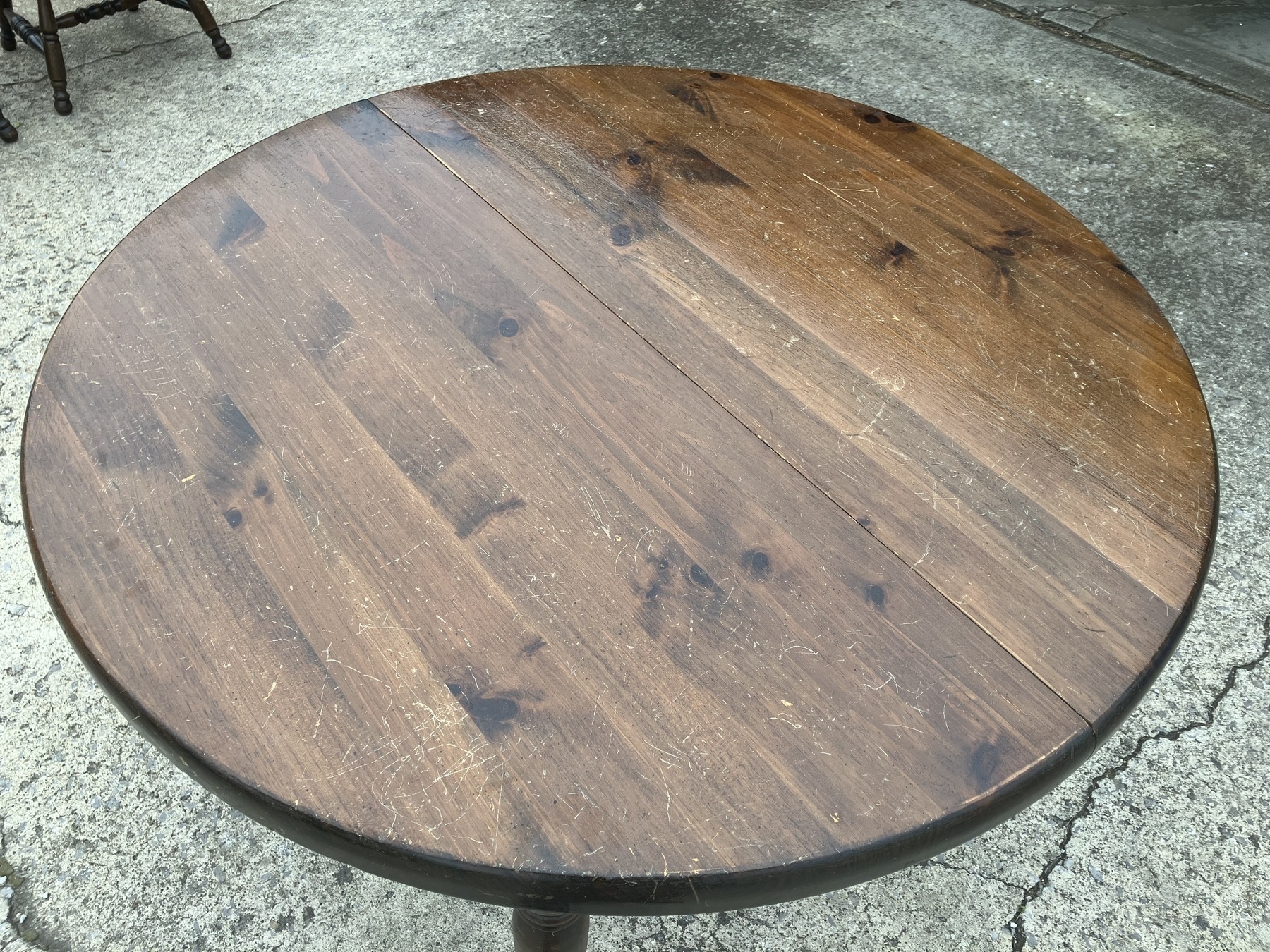
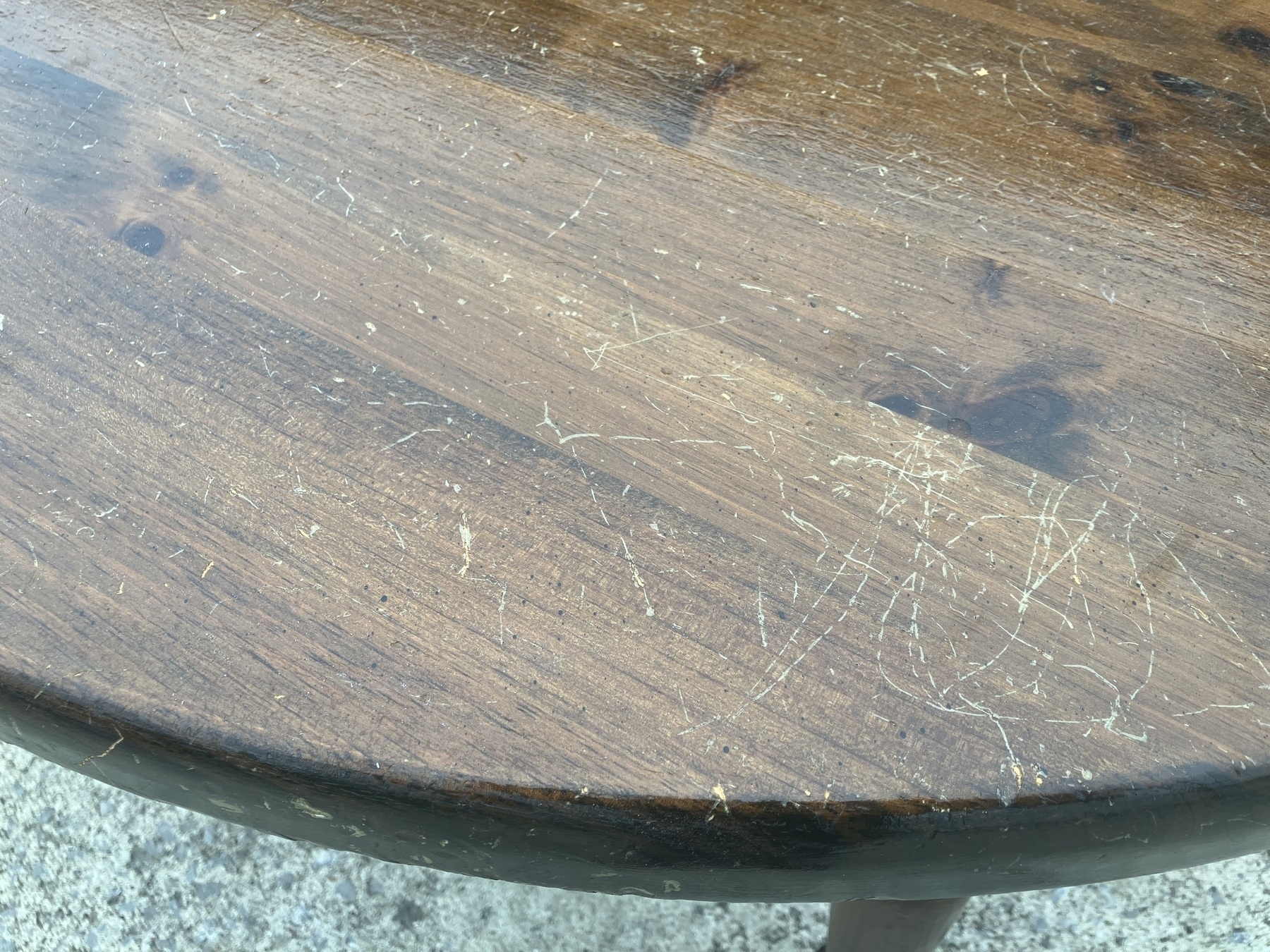
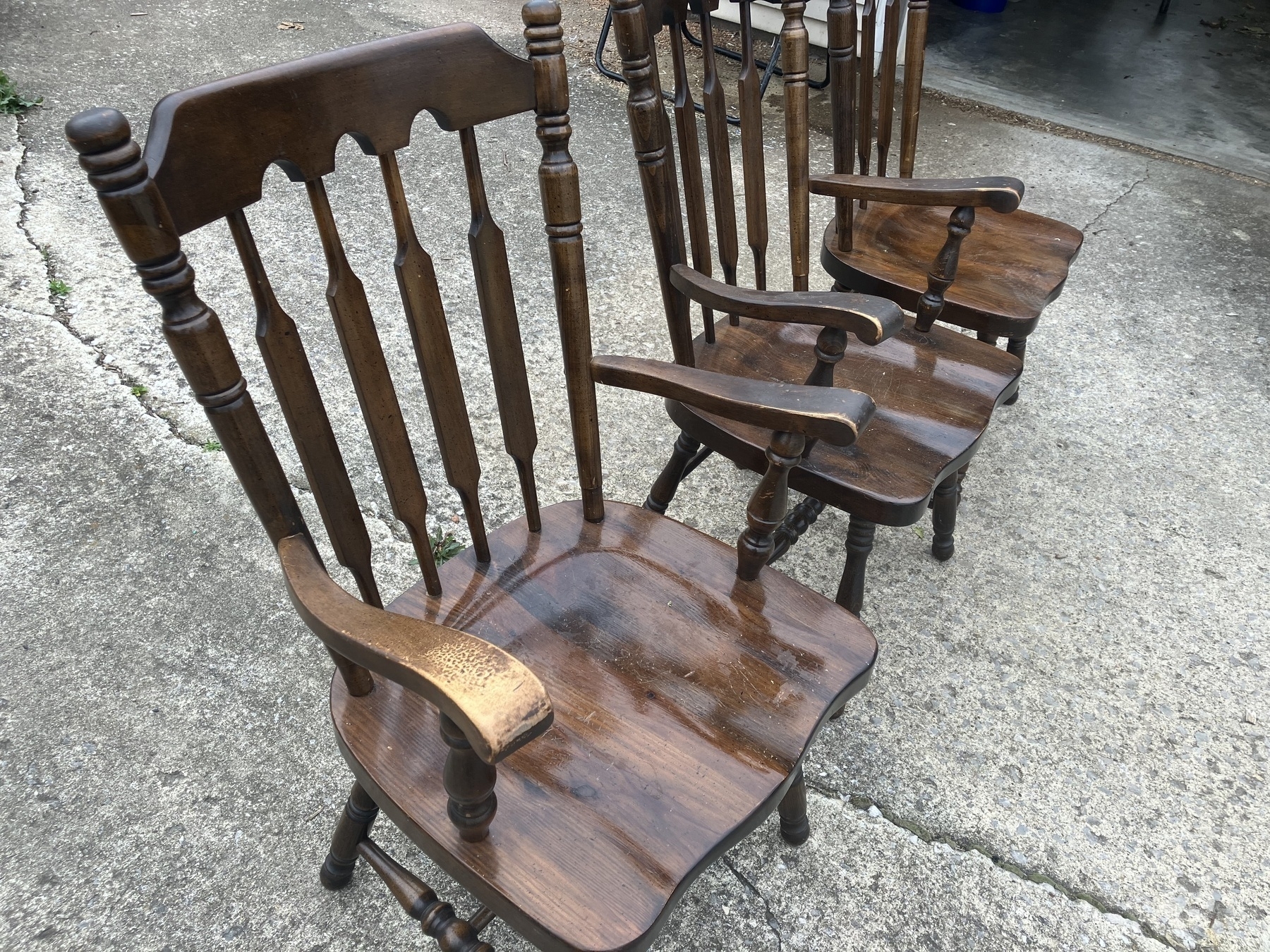
After:
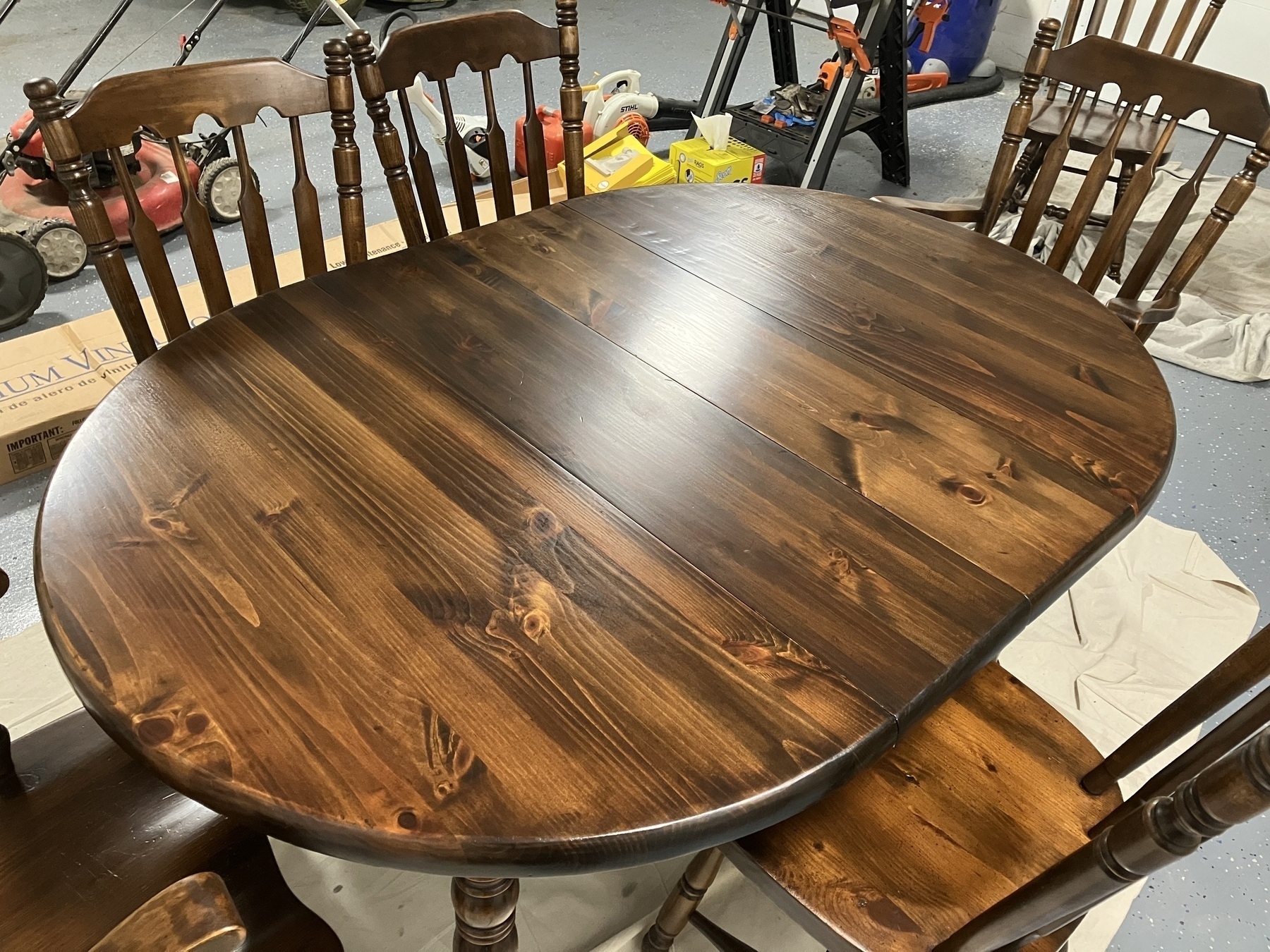
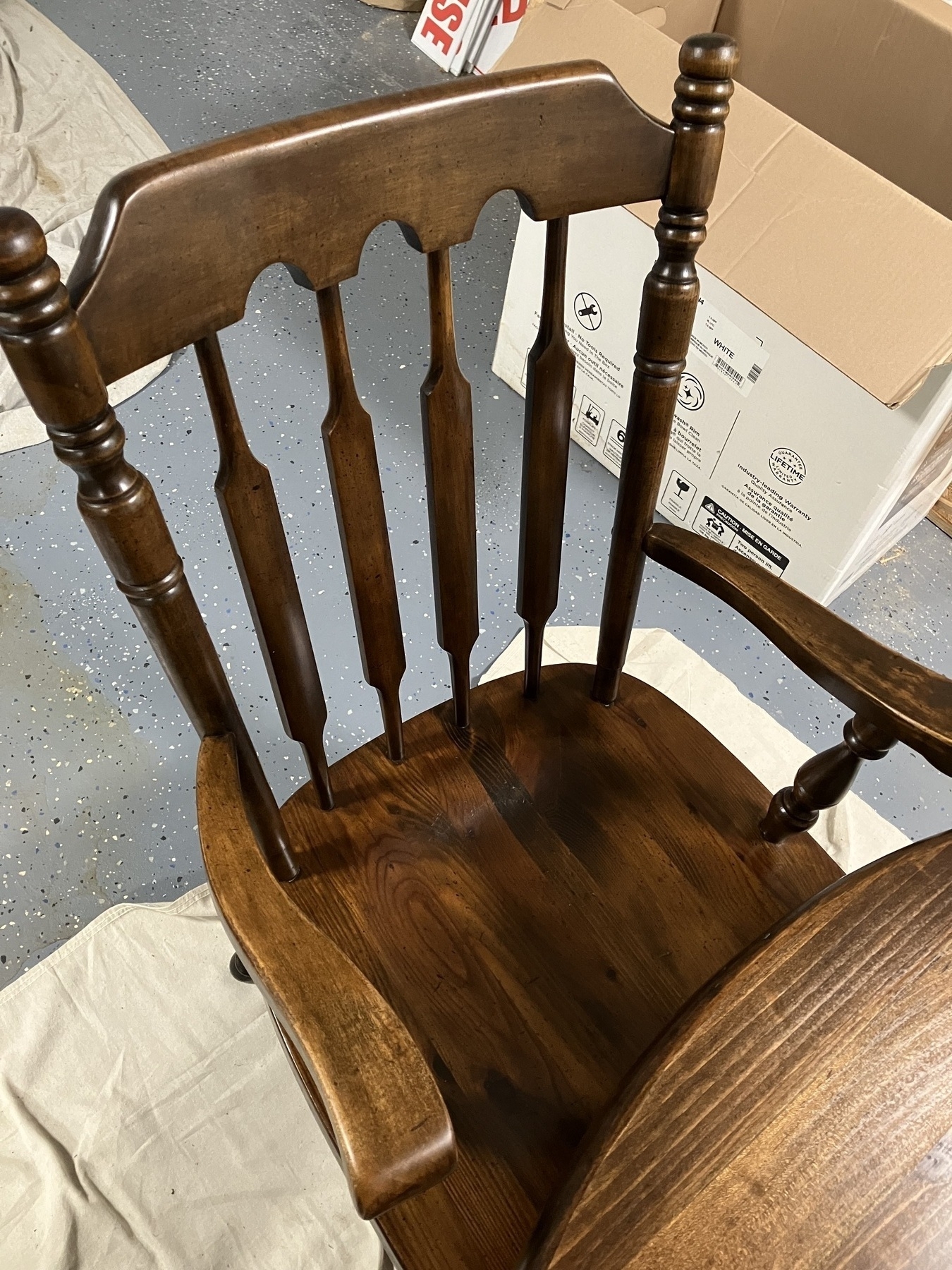
I mentioned recently that this apocalyptic humidity is wreaking havoc on the finish on the table and chairs I’m working on. The lovely and talented Rachel came up with a great solution: finish them in her parents’ garage, which is climate controlled. They agreed and the finish is looking better.
This humidity we’re having. My in-laws want a polyurethane finish on their table and chairs. When I spray a coat on a chair it goes cloudy. (I’m doing this in my detached garage with no AC.) So I’ve brought a chair in to my nasty but climate controlled basement and will try it there. Fingers crossed
I’m nearing the end of the table and chairs restoration project for my in-laws. It’s taking me a long time—thankfully they’re not in a hurry. I’ve had to learn a lot as I go. But now that I can see the end, I’m planning more restorations. Like this rocker. Looks like I’ll be learning rush weaving!
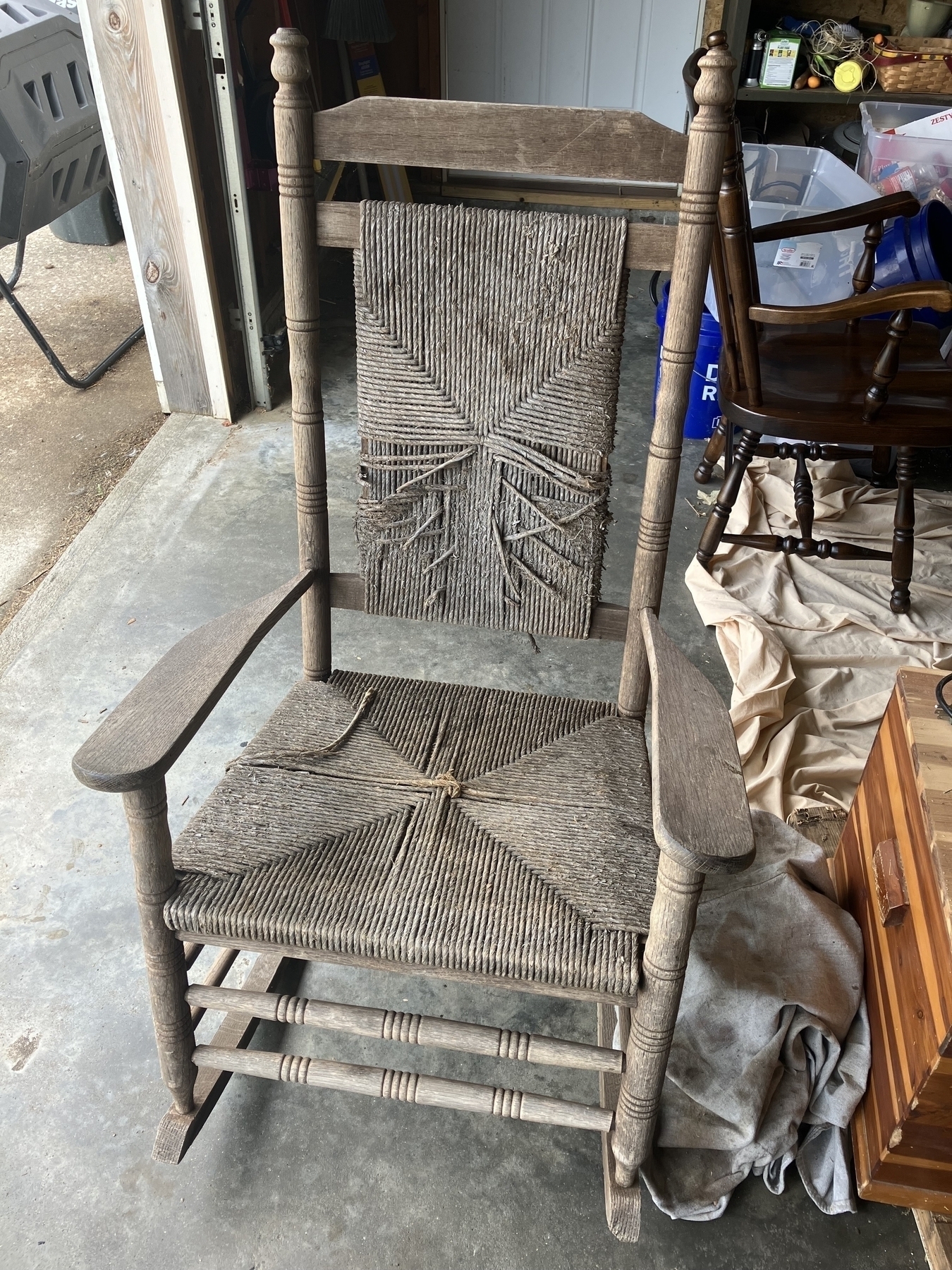
As if I wasn’t already behind on my projects, I picked up a chair today for $5. I don’t know anything about identifying chair styles or age. Obviously that square of wood nailed to the top of the seat isn’t original. Maybe it used to have a drop in seat or was a rush seat?